One of the biggest crises societies around the world face is building affordable homes for growing populations. Rising building costs and a workforce shortage exaggerate the inefficiencies of the construction industry, which has been notoriously slow to digitise.
These are big problems, but one UK-based startup, Automated Architecture — or AUAR (pronounced ‘our’) for short — thinks it has a solution that could help tackle them. And it’s just raised £2.6m to kickstart plans to build affordable homes across Europe and the US.
The round was led by venture studio Miles Ahead and featured ABB RA Ventures — the VC arm of automotive robotics company ABB, Rival Holdings and Morgan Stanley.
AUAR is automating the construction process of timber houses with robots in small production facilities — which it calls “microfactories”. Combined with a proprietary operating system, the startup can strip back the thousands of production lines usually involved in the building process to just a couple, says cofounder and CEO Mollie Claypool.
According to Claypool, AUAR can save constructors on labour and supply chain costs, as well as encourage more sustainable building practices via the use of greener materials and reduced transport on the roads.
“If we can get construction companies to radically change the way they engage with technology, we can deliver high-quality affordable housing at scale,” she says.
Robots to build our homes
For AUAR, that process hasn’t begun by building houses. The startup’s single operational microfactory is in Gent, Belgium and has been used to build a number of interior spaces for a new coworking space and tech hub in the region.
It’s one of several small projects AUAR has used to prove its building tech works — which have also brought in a small amount of revenue — but the startup is finalising another microfactory in Indiana, US, which will be used to build homes.
AUAR has developed a building system that involves making wooden pieces that fit together to create timber houses up to six stories high — like walls, roofs and ceilings — in “blocks” in microfactories.
Robotic arms cut and assemble the materials, before they’re put together “like lego” by humans either in the microfactory or on a construction site, says Claypool.
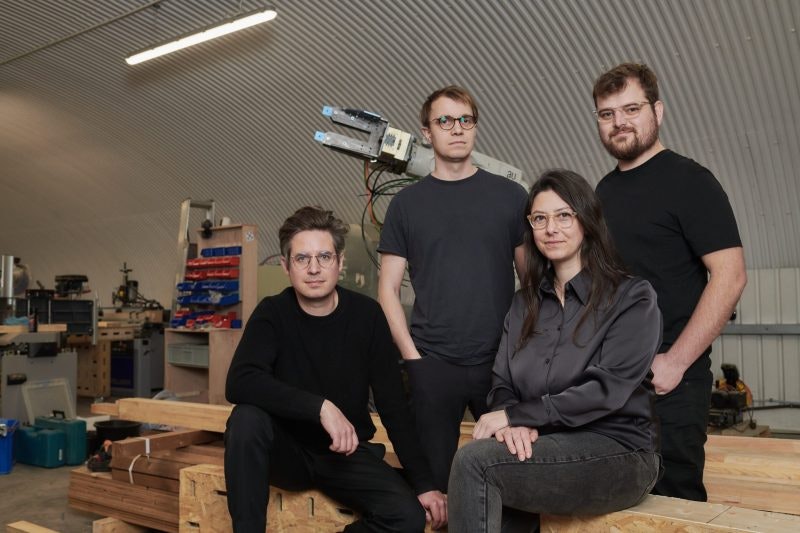
The arms are off-the-shelf products made by its investor ABB — designed for the automotive industry — but AUAR has developed specific hardware like a hand that allows the robot to interact with the materials and workstations that it operates on.
There’s also an software which architects can use to design a house that streamlines construction and price information in one place.
AUAR licences its hardware and software out to larger construction companies. They pay an upfront cost of around £250k to install the microfactory — which sits within a company’s industrial site — and a monthly fee that covers troubleshooting and servicing the hardware. If the use of a microfactory goes above a certain level, licensees pay an additional fee which can be up to 10% of that extra revenue.
Typically, an architect does the design and then the contractor puts together the costing, before a “haggling” process that can take months, Claypool says. “We’re automating it. Upfront, architects can know the design decisions and contractors get an automated list of materials, costings and production timelines.”
Saving money — and the environment
AUAR is hoping to attract construction companies with the allure of efficiency and — as regulation increasingly forces builders to reduce pollution — emissions savings.
“The average home has about 7000 parts — each with a different supply chain,” says Claypool. “We have one primary material, and only a few supply chains.”
According to Claypool, the robots building the house blocks can work five times faster than a human and AUAR’s building system can cut labour costs by 30% and supply chain, transport and logistics costs by 80%.
Fewer lorries on the roads shipping parts between sites also means lower emissions, she says.
The construction industry is one of the most polluting in the world — in the UK, building work is responsible for 18% of particulate pollution.
But building with timber could go some way to bringing that figure down. According to the UK government, using timber can reduce the emissions in a single building by 20% to 60%. Each of AUAR’s microfactories can save 5m tonnes of emissions, says Claypool.
Despite that, there’s a fear that “timber is a degrading material”, she says, adding that it can be if left exposed and untreated.
“But if you cover it well and maintain that facade it can last for hundreds of years, which is longer than many [brick and mortar] buildings last,” Claypool says.
The rise of construction tech
AUAR is one of a growing number of construction tech companies that have picked up VC cash in recent years as the traditionally tech-averse industry has — albeit at a snail’s pace — looked to digitise to make efficiency savings.
In Europe, 2023 was a record year for funding in the sector, with startups picking up $759m — just shy of the $795m they raised in the decade up to 2020.
Founded in 2019, AUAR’s fresh capital is its first round of external funding, and the startup plans to open up a third microfactory — probably in the UK, according to Claypool — by the end of this year.
The funding will last around 18 months, and AUAR wants to install microfactories on 10 more construction companies’ sites in that time. It’s in conversations with companies in the US, UK, Spain, Portugal, the Netherlands and Canada, says Claypool.
By 2030, it wants to have partnered with 40 microfactory customers and built 75,000 homes.